Concrete is a durable material, but it shows wear and tear over time. Heavy foot traffic and vehicles, harsh weathering, ground movement, and aging can cause structural damage that requires repair.
It’s important to choose the right repair methods and materials for your concrete project’s conditions and performance needs. Incorrect choices may lead to recurring problems and safety hazards. Contact Concrete Repair Dallas now!
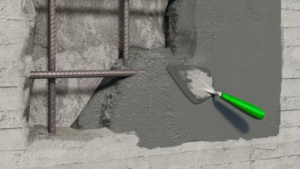
Concrete is durable and strong, but it will eventually crack. Cracks are unsightly and can lead to a loss of structural integrity if ignored. Luckily, proper maintenance and repair techniques can keep these issues at bay.
The first step to crack repair is to clean the crack. A pressure washer or detergent can make this task easier by removing any debris stuck in the crack. It’s also important to determine whether the crack is active or dormant. An active crack may be at risk of causing further damage and should be addressed immediately, while a dormant crack is stable and only needs to be monitored.
Once the crack is cleaned, a thin layer of bonding adhesive can be applied. This step ensures the crack filler adheres to the concrete surface. A masonry sealant or epoxy can be used to apply the glue. Once the sealant dries, the crack can be filled with a concrete patching product. Different products require different applications, so it’s important to follow the instructions provided by the manufacturer.
When using a concrete crack repair product, it’s important to mix the ingredients well and apply them consistently. The product will “settle” into the crack over time, so be sure to apply a second layer as needed. Once the second layer dries, it’s important to smooth the crack with a putty knife or mason’s trowel.
Cracks in concrete surfaces pose trip hazards for people on foot. Not only do they look unattractive, but they can catch shoes or cause people to stumble. By filling these cracks, you can prevent injuries on your property and create a safer environment for everyone who visits.
After the crack has been repaired, a protective coating should be applied to protect the area from further damage and prolong the life of the concrete. Water-based acrylic, epoxy, and polyurethane are a few common choices for this application. Each has its benefits, so be sure to choose the one that best suits your needs. It’s also a good idea to spread a tarp beneath the work area to facilitate cleanup.
Joint Sealant
The final step in concrete repair involves applying a joint sealant. This is important to prevent leaks and help the repairs last longer. It is also crucial to make sure that the joint sealant used is compatible with any materials that may come into contact with it. It is a good idea to have the sealant manufacturer provide compatibility testing prior to use.
In general, it is a good idea to try and match the joint sealant with the concrete surface it will be used on. This will prevent premature failure of the sealant due to poor adhesion. It is also a good idea to use proper surface preparation techniques to ensure that the bonding between the sealant and concrete is strong. This includes removing any contaminants and thoroughly cleaning the surface to ensure that the sealant will adhere well. It is also a good idea to sand the surface of the concrete and apply a primer to prepare it for the application of the joint sealant.
For most applications involving movement joints it is important to use a sealant that has been tested for outdoor weathering and movement. Many engineering firms, contractors, and sealant manufacturers will perform this test (ASTM C794) on a sample of their product in their labs. This will help them determine which sealants will perform best in the given climate.
This test consists of sealing the joint, letting it cure and then extending the joint to +25%, holding it there for five minutes and examining the joint for adhesive and cohesive failure. This is one of the most rigorous tests and yet it is a standard test that many consider too lenient for what should be the highest quality sealants.
There are a few exceptions to this rule though. Some urethanes, silicones and polyureas are able to handle a higher amount of movement than what is outlined in this test. These types of sealants can be tested using an alternative ASTM method that uses only a single extension movement cycle. This is often referred to as the painter’s caulk test and allows for up to 25% of either adhesion or cohesive failure.
Stitching
The goal of concrete repair is to restore and strengthen existing structures, keeping people and assets safe and secure. Concrete restoration services are a cost-effective alternative to tearing down existing structures and building new ones. They also reduce environmental impact and minimize waste production.
Stitching is a rehabilitation technique that is used at cracks to maintain aggregate interlock and provide added reinforcement to minimize relative movement of concrete slabs. It’s a great solution for large concrete cracks and for areas where the structural capacity is nearing its limit. However, it’s important to fix the underlying cause of the cracking before stitching can help. Otherwise, the cracks will reappear and your structure may experience further damage.
When selecting a concrete repair material, consider the dimensional characteristics of the concrete and the environment where the repair will be placed. For instance, moisture content and temperature can affect how a repair material sets. It is essential that a concrete repair material has similar properties to the original concrete for the most successful repairs.
Many repair materials use different types of polymers that increase bond strength and durability. This is especially true for high-performance concrete repair materials that incorporate various types of fibers. These products can be used for general purpose concrete patching as well as in-situ applications like grouting or injection into cracks.
Concrete restoration is a complex process, and it’s important to have the right tools on hand for the job. A quality concrete restoration tool kit includes all the necessary supplies to complete a project and maximize your investment. The most important items are a hand trowel, gloves, masonry sand, and a good quality concrete mix. When working on a concrete repair project, there are some mistakes that you should avoid making to ensure the best results.
For example, skipping surface preparation can lead to poor adhesion and recurring problems. Incorrectly using a product or application method can also derail the success of your concrete repair project. It’s also important to allow adequate time for the repair to cure.
In addition to these common concrete repair mistakes, there are several other factors that can negatively impact the life-cycle sustainability of concrete structures. These factors include escalating maintenance costs, natural resource depletion, and pollution from inert construction waste and air emissions. Engineers have an important role to play in designing eco-efficient concrete repair systems that meet specified performance levels for the desired service conditions.
Epoxy Injections
Epoxy injection is a method for repairing cracks and voids in concrete structures. It uses two-part epoxy resin, which creates a strong bond between the crack surfaces. This bond helps transfer loads, preventing further crack propagation and structural damage. It is also moisture resistant, making it an ideal solution for concrete repair in areas that are exposed to water or high humidity. It is best used for non-moving cracks in concrete walls, slabs, and columns. It is typically used in conjunction with internal and external reinforcement for structural strengthening.
Epoxy crack injection is a minimally invasive procedure, requiring only small holes to be drilled for injection. This allows the process to be completed quickly and without causing any interruptions to business or operations. It is a cost-effective repair solution when compared to extensive replacement of the damaged concrete structure.
The first step in preparing for epoxy injection is to clean the crack and surrounding area thoroughly. This is done to remove any dirt, debris, or contaminants that may interfere with the adhesion of the epoxy and concrete. Injection ports are then installed along the length of the crack, at regular intervals. The injection ports, which can be surface mount or socket mount ports, are then bonded to the concrete using epoxy paste.
Once the injection ports are in place, the epoxy is mixed according to the manufacturer’s instructions. Once the mixture is ready, it is injected into the crack through the injection ports. As the epoxy is injected, it spreads across the crack, filling the void and restoring its integrity. Once the epoxy has been injected, it is allowed to cure for the recommended time. After curing, the injection ports are removed and the cracked surface is smoothed to match the surrounding surface.
Before performing this type of crack repair, it is important to understand that epoxy injections are primarily intended for structural issues. It is not a suitable solution for leaking cracks, as the epoxy will not displace or react with water. In fact, water seepage can actually cause the epoxy to leak through the repaired crack.